Günlük hayatımızda kullandığımız birçok ürünün üretiminde kalıplar kullanılmaktadır. Kalıplar ile talaşlı üretim yöntemiyle elde işlenmesi zor olan veya imkânsız olan karmaşık birçok parçanın üretimi kolaylıkla yapılmaktadır. Örneğin; evimizde kullandığımız tencereler, elimizden düşürmediğimiz telefonların gövdeleri, araçlarımızda kullandığımız alüminyum jantlar bu kalıplarla üretilmektedir. Ölçü ve profil olarak birbirine benzeyen veya aynı parçaların seri şekilde üretilmesinde kullanılan bloklara “kalıp” denir. Kalıpçı ise, yapım aşamasında istenilen zaman, kalite, profil ve ölçüde kalıpların üretimini işçilik, malzeme ve diğer giderleri minimum düzeyde tutarak yapan kişilerdir. Tüm bu işlemler, teorik ve uygulamalı eğitimle birleşerek kalıpçılık mesleği oluşmuştur.
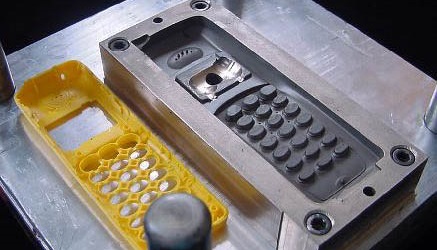
Kalıpla üretimin avantajları nelerdir?
- Büyük parça adetlerinin üretilebilirliği
- Birim maliyetin düşmesi
- Hızlı ürün akışı
- İşgücünden tasarruf
- Otomasyona uyumluluk
- Tek işlemde istenilen ölçü, kalite ve profilde üretim
- Küçük parçalar için ideal yöntem olması
- Diğer yöntemlere göre daha hızlı üretim
- İstenildiğinde aynı anda çoklu üretim (conta üretimi gibi…)
- Yedeklenebilme sayesinde kesintisiz üretim
- Tekrarlanabilen aynı parça üretimi
- Yeterli korunduğunda ve bakımı yapıldığında uzun süre dayanım
- Aynı anda birden fazla işlemin sağlanabilmesi (Profil verme ve aynı zamanda çevre kesme gibi…)
- Küçük revizyonlarla farklı parçaların üretimine izin vermesi
- Diğer yöntemlerle üretilemeyen çok karmaşık yapılardaki parçaların üretimine olanak sağlaması
Kalıpların dezavantajları nelerdir?
- İlk etapta yüksek kalıp maliyeti
- Kalıpların bağlanacağı ekipman ve tezgahların pahalı olması
- Hatalı işlemlerde kalıpların tek seferde hurdaya ayrılması(dişi erkek kalıbı bindirme gibi…)
- Bazı kalıplarda ayar sürelerinin uzun olması
- Operatör bilgisinin eksikliğinden kaynaklı kalıp ömrünü azaltan etmenler
- Kalıplardaki istenilen revizyon neticesinde bazen kalıbın yeniden üretilmesi
- Yedekleme işleminin pahalı olması
- Kalıp üretiminin uzun sürmesi,
- Bozulan kalıp yerine yenisinin üretiminin çok zaman alması
- Çok büyük çaplarda malzemelerin üretiminin kalıplarla çok zor ya da imkânsız olması
Kalıp çeşitleri nelerdir?
1. Plastik Kalıpları
- Plastik enjeksiyon kalıpları: Küçük çaptaki plastik hammaddenin(plastik granül) eritilip, yüksek basınç altında kalıba enjekte edilerek uygulandığı kalıp türüdür. Bu kalıpta erimiş plastik malzeme kalıp içerisinde soğuyarak çok kısa bir sürede son şekline gelir. Hassas plastik malzemelerin üretiminde iyi sonuç verir. Ayrıca kalıptan hatalı çıkan parçaların tekrar eritilerek kullanılması sayesinde fire oranı yok denecek kadar azdır. Çeşme contaları buna örnek verilebilir.
- Termoset kalıbı: Termoset ve kompozit plastikler kalıp içerisinde yüksek ısı ve basınç altında pişirilerek son şeklini alır. Kalıptan çıkan ürünlerde çapaklar ve fazlalıklar oluşur ve bunlar talaşlı üretim yöntemleriyle temizlenir. Ayrıca hatalı üretilen ürünlerin pişirilip tekrar soğuduğundan ve içyapısı değiştiğinden dolayı tekrar geri dönüşümü yoktur. Çaydanlık tencere tutamakları ve elektronik parçalar örnek verilebilir.
- Termoform (Vakum) Kalıpları: Isı ile şekil değiştirebilen düz bir plastik (termoplastik) levha ısıtılır ve vakumlanarak(emme işlemi) kalıbın şeklinin alması sağlanır. Separatör ve bazı plastik paletler bu yöntemle üretilir.
- Şişirme (Blow Mold) Kalıpları: Pet şişelerin üretimi bu kalıplar için güzel bir örnektir. Isıtılmış ama erimemiş bir plastik bir tüp kalıp içerisine yerleştirilir. Ani ve çok yüksek basınçlı hava plastik tüp içerisine verilir. Kalıbın şeklini alır.
- Ekstrüzyon kalıbı: Plastik boru ve kablo gibi uzun ve sürekli parçaların dökülmesi için bu yöntem kullanılır. Eritilen bir plastik kalıp içinden sürekli olarak akıtılır ve ani soğutulur. Kalıp kanal şeklindedir. Soğutma olarak su ve hava kullanılır.
2. Metal Enjeksiyon Kalıpları:
Alüminyum, pirinç, magnezyum ve kurşun gibi ergime sıcaklığı çok yüksek olmayan malzemeler granüller halinde ergitilerek üretiminde kullanılır. Yüksek basınç yardımıyla kalıplara enjekte edilerek kalıp içerisinde soğuma sağlanır. Bu enjeksiyon kalıpları sıcak ve soğuk kamara olarak iki çeşit preste kullanılır. Karmaşık yapıdaki metal parçaların hassas şekilde üretimi sağlanır.
3. Metal Form Verme, Kesme ve Sıvama Kalıpları:
Sac ve metal levhaların yüksek basınç altında kalıbın şeklini aldığı yöntemdir. Bu yöntem işlemin türüne göre isim alır. Sıvama, kesme kalıpları gibi… Seri üretim için idealdir. Sıvama kalıpları genellikle çok keskin profili olmayan parçalarda uygulanır. Çünkü metal levhanın yırtılma riski mevcuttur.
4. Dövme Kalıpları
Belirli sıcaklığa getirilen metal parça dövme işlemi yapılarak kalıbın şeklini alır. Örnek olarak, bazı şaftlar ve büyük açıkağız anahtarlar, cıvata başları verilebilir.
Eğer bir kalıp yapmaya karar verdiysek; yapılacak olan kalıbın öncelikle maliyetleri, kullanılacak malzemeler, ne kadar gerekli olduğu ile ilgili fizibilite çalışması yapılması gereksiz yere pahalı ve çok kullanılmayacak kalıpların yapılmasının önüne geçer. Ayrıca çıkacak ürünün hassasiyeti, kalitesi ve geometrisi kalıp maliyetini etkileyen unsurlardır. Kalıp üretiminde işin başında bulunan kişiler (kalıpçılar) kalıpla ilgili bilmesi gereken özellikleri bünyesinde barındırası ya da öğrenmesi gereklidir.
Hiç yorum yok:
Yorum Gönder
İş yoğunluğum dolayısıyla yorumlara cevap veremeyebilirim. Anlayışınız icin teşekkürler.